Как шьют женское бельё The Village побывал на фабрике, где шьют трусы и бюстгальтеры
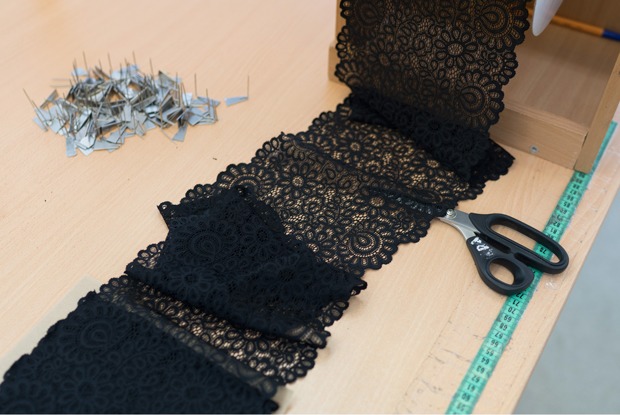

Фотографии
яся фогельгардт
Компания «Дикая орхидея» работает на рынке с 1993 года, тогда открылся первый магазин с таким же названием. После собственник поменялся в 2012 году, и «Дикая орхидея» стала «Розтехом». Сейчас, помимо нижнего белья, на трёх фабриках компании шьют купальники, домашнюю одежду, трусы и бюстгальтеры для магазинов «Дикая орхидея» (премиум), «Бюстье» (средний сегмент) и «Дефиле» (масс-маркет). Всего здесь работают около 2 тысяч человек и производят более 2 миллионов единиц продукции в год. The Village узнал, как разрабатываются новые модели и как их потом шьют.
Разработка коллекции
Экскурсию мы начинаем с головного офиса компании, который находится в трех километрах от Москвы: сотрудники едут на работу на корпоративных маршрутках от метро «Полежаевская». Во дворе офиса всех встречает памятник Ленину, выкрашенный в бронзовый цвет. Его голова блестит на солнце, что делает его похожим на статую Будды.
Офис занимает шесть этажей, мы начинаем с третьего, где сидит отдел разработки — именно здесь придумывают новые коллекции. Сейчас здесь работают 25 человек, среди них конструкторы, дизайнеры и продакт-менеджеры. В основном работают здесь девушки, мужчин можно увидеть разве что в IT-отделе. В целом обычный офис, не считая одного — нижнее бельё здесь лежит на столах, висит на перегородках и на вешалках. И, кажется, нет ни одной стены, на которой бы не был пристроен плакат с моделью в белье или купальнике. Правда, компания «Розтех» производит не только эту продукцию, но ещё и домашнюю и пляжную одежду, а вся продукция продается в трех сетях: «Дикая орхидея», «Бюстье» и «Дефиле» под разными брендами, среди которых Wild Orchid, Savoia, Beatrice, Vendetta, Croisette, Mysticite, Defile, Lavinia.
Над новым сезоном работа начинается за полтора года, например, сейчас отдел разработки трудится над созданием коллекций для лета 2017 года. Отправная точка — это первая презентация, на которой и сотрудникам, и заказчикам представляют анализ мировых трендов в белье и купальников. Дизайнеры собирают всю информацию об одежде, аксессуарах, обуви, купальниках, нижнем белье и рассказывают о том, что будет актуальным в новом сезоне. Затем закупщики каждого бренда составляют техническое задание, в котором указывают количество линий (например, десять линий нижнего белья и столько же купальников), коллекций, обозначают желаемые цвета, стиль и передают эту заявку дизайнерам.
На основе этого дизайнеры составляют презентации, для которых они делают наброски первых моделей. Могут иногда даже попытаться сделать бельё из тех материалов, что есть: например, наколоть булавками новую ткань на чашечку. На подготовку второй презентации уходит около месяца. На ней закупщики согласовывают некоторые идеи, какие-то модели просят переделать или что-то добавить. И в течение трёх месяцев дизайнеры готовятся к следующей презентации, на которой представляют уже полностью доработанный и отрисованный модельный ряд.
Параллельно конструкторы разрабатывают лекала, швеи в лабораториях отшивают первые образцы — прототипы, чтобы закупщик видел не только прорисованные коллекции, но и то, как бельё сидит на модели, то есть выглядит в реальности. Для модели в офисе даже есть специальная комната. Забавно, что образцы иногда отшиваются в «родных» тканях, но не в тех цветах, в которых будет коллекция: у поставщиков не всегда есть в наличии желаемый цвет. «Мы привыкли, что видим белый, а представляем, что это чёрный», — рассказывают сотрудники. Сроки зависят от сложности модели и самой технологии, поэтому на тот образец, который сделан с нуля, может уйти три-четыре дня, а если модель несложная, то можно успеть и за день.
После второй презентации заказчик говорит, какие линии, в каком количестве и каких цветах он берёт. И позже начинается работа по созданию этой партии нижнего белья. Материалы приезжают примерно через полгода — из европейских стран для «Дикой орхидеи» и из Китая для остальных сетей, а за это время в компании разрабатывают лекала на все размеры, прорабатывают технологию, чтобы шить каждую модель было максимально быстро и удобно. Перед тем как пустить что-либо в массовое производство, в компании шьют опытные партии — это 40 разных артикулов, которые раздают внутри компании и отправляют партнёрам марки. Люди в течение нескольких дней носят это бельё, чтобы понять, насколько оно удобно, и стирают, чтобы посмотреть, как материал будет вести себя после стирки, и дают свои комментарии.
В целом в коллекциях нового сезона всегда есть несколько направлений: volume drivers (базовые продукты, которые обеспечивают основной объём продаж), must-have (тренды сезона) и high risk — это инновационные продукты, которые выпускаются небольшими партиями, и если они хорошо продаются и остаются актуальными на следующий сезон, то их включают в основную линейку. Помимо этого, есть базовые модели, которые компания выпускает каждый сезон, но в новом цвете или с другой отделкой или декором. Самые ходовые размеры бюстгальтеров— 75В и 75С, лидер продаж — конечно, чёрный цвет, но к лету возрастают продажи белого белья.
Массовое производство
Чтобы узнать, как шьют нижнее бельё, мы едем дальше, на фабрику в Гагарин, на родину самого знаменитого советского космонавта. Памятников Юрию здесь хватает, а вот дороги толковой нет, наша машина уворачивается от кочек и заезжает в частный сектор. Наконец среди невысоких домов мы видим здание, обшитое материалом бордового цвета. Это и есть та фабрика, которая нам нужна. Нас встречает ответственный сотрудник и провожает в переговорную. Одна из стен переговорной выглядит как витрина с купальниками, а остальные украшены фотографиями в тяжёлых рамах — они висели в первом магазине, открытом компанией. На производство мы торопимся: в 16:00 будет пересменка, а мы приехали за час до неё.
Для того чтобы запустить партию, нужно подготовить ткань и убедиться, что она хорошего качества и без дефектов. Для этого каждый рулон материала закладывают в мерильно-браковочную машину, которая перематывает его на фоне белого экрана —так ткань разбраковывается. Сотрудник просматривает полотно на просвет; кроме того, машина измеряет, соответствует ли ткань указанному метражу. Если работник заметил какой-то дефект, то отмечает его стикером. В среднем для отшива массовой партии нижнего белья — 6 тысяч штук — нужно около 500 метров ткани.
Для эластичных материалов нужен ещё один этап: перед раскроем они должны сутки просто лежать в размотанном виде. Рулон материала автоматически разматывается, и на то, как струится ткань, можно смотреть бесконечно. Если этот этап исключить, то после раскроя детали могут сесть и изделие получится меньшего размера, чем планировалось.
На следующем этапе — раскройном участке — ощутимо более шумно, чем на предыдущем. Раскройка кружева и ткани отличается. С кружевом приходится работать только вручную — ни по ширине, ни по рисунку оно не бывает стабильным: где-то узор чуть расслабленнее, где-то туже.
Прежде чем разделить на детали, кружево сначала утюжат, затем складывают слоями и скрепляют иголками в соответствии с рисунком: важно, чтобы чашечки в бюстгальтере были идентичными. Затем на кружево накладываются лекала, и раскройщица вырезает детали на раскройной ленточной машине. На оборудовании установлен быстро вращающийся нож, который со стороны выглядит как металлический штырь. Раскраивать кружево нужно в специальных перчатках, собранных из мелких металлических колец — настоящая кольчуга для рук. Правда, сотрудники на них жалуются: перчатки тяжёлые, и работать в них очень неудобно.
С тканью мороки меньше, её раскраивают на автоматическом раскройном комплексе. Сначала ткань нужно настелить и разрезать на 20 слоёв. Обычно на фабриках с этим справляются два сотрудника: оттягивают от рулона нужный кусок и отрезают. Но опять же из-за эластичности материала тут такой номер не пройдёт. Поэтому рулон подают на настилочный комплекс, задают нужную длину одного слоя, затем машина разматывает рулон и настилает ткань слой за слоем — ткань стелется свободно, безо всякого натяжения. Снизу подаётся перфорированная бумага, которая пригодится на следующем этапе — на раскройном автоматическом комплексе.
После разрезания всех слоёв на ткань кладётся маркер — бумага, на которой напечатана раскладка. Ткань скользкая, поэтому для того, чтобы её разрезать, нужно для начала каким-то образом её закрепить. Для этого сверху и снизу кладут перфорированную бумагу, которая после с включением вакуума прижимается к столу, и все 20 слоёв материала становятся практически тонким пластом. И затем машина вырезает ткань ровно по той раскладке, которая настелена сверху, так как в неё все данные о ней загружены.
Комплектовщики складывают детали с лекалами, формируя пачку кроя, а лишние обрезки выбрасывают. Работа кропотливая: важно не ошибиться и, например, не перепутать детали второго размера с третьим. Кроме деталей из микрофибры, в лифе будут ещё детали из других материалов, которые тоже должны складываться в эту же пачку кроя. Всё, что скомплектовано, упаковывается в коробки и отправляется в швейный цех.
Но прежде чем идти туда, мы видим ещё одну операцию — формование, которое проходят ткани для чашки бюстгальтера, потому что в готовом виде они должны быть гладкими. Всё это происходит на молдере: сотрудник берёт вырезанную ткань для чашечек, кладёт на отверстие в аппарате и прижимает его специальной формой, а через десять секунд вместо плоской ткани достаёт выпуклую. Такой пузырь получается благодаря давлению и высокой температуре. Теперь такую ткань можно надеть на поролоновую чашечку и пришивать, не делая вытачек. Для каждого размера есть свои формы — они металлические, похожи на снаряды, лежат на стеллаже неподалёку от молдера.
Табличка «Перевозка людей запрещена» возле лифта намекает на то, что подниматься на третий этаж в швейный цех придётся пешком. Здесь будто свой небольшой город — шумно и много людей: в одну смену здесь работают 120 сотрудников. На входе стоят несколько одетых манекенов — на них надето то, что сейчас шьют на производстве. В этот цех поступают пластиковые коробки с тем, что раскроили на предыдущих участках. К каждой пачке кроя прилагается маршрутный лист, в котором указан размер, цвет и последовательность всех операций, которые надо проделать, чтобы из кусочков ткани получить готовый бюстгальтер или трусы.
В швейном цехе работа идёт пооперационно, то есть сотрудник, во-первых, соблюдает указанную последовательность, во-вторых, выполняет одну или несколько операций и передаёт продукт дальше, на следующую станцию. Конечно, бельё передаётся не поштучно, а партиями по 20 штук. Начинается обычно всё с того, что нужно сделать отметки на чашке бюстгальтера, чтобы позже по ним сшивать. Интересно, что бюстгальтеры последовательно шьют на одной ленте, получается такая бельевая гирлянда, которую потом разрезают. Всё сшивается по таблице измерений, чтобы ни в коем случае не уйти в другой размер. В основном всё делается при помощи оборудования; исключения делаются, только когда нужно завязать бант или вставить металлические каркасы.
Готовое бельё отдают ручницам, которые с помощью ножниц-щипцов убирают все лишние нитки. Потом продукт передают контролёру, который проверяет каждую модель: всё ли выполнено верно и не закралась ли где-то ошибка в измерениях. Затем ручницы упаковывают нижнее бельё в пакеты и складывают в коробки. Всё это поступает в зону отгрузки, а потом партию спускают на второй этаж, на склад. И уже со склада новое бельё попадает в магазины.
Чтобы прочитать целиком, купите подписку. Она открывает сразу три издания
месяц
год
Подписка предоставлена Redefine.media. Её можно оплатить российской или иностранной картой. Продлевается автоматически. Вы сможете отписаться в любой момент.
На связи The Village, это платный журнал. Чтобы читать нас, нужна подписка. Купите её, чтобы мы продолжали рассказывать вам эксклюзивные истории. Это не дороже, чем сходить в барбершоп.
The Village — это журнал о городах и жизни вопреки: про искусство, уличную политику, преодоление, травмы, протесты, панк и смелость оставаться собой. Получайте регулярные дайджесты The Village по событиям в Москве, Петербурге, Тбилиси, Ереване, Белграде, Стамбуле и других городах. Читайте наши репортажи, расследования и эксклюзивные свидетельства. Мир — есть все, что имеет место. Мы остаемся в нем с вами.