СпецпроектыГлина, огонь и роботы: Как в Екатеринбурге делают плитку с итальянским качеством
И правда ли плитку декорируют настоящим золотом
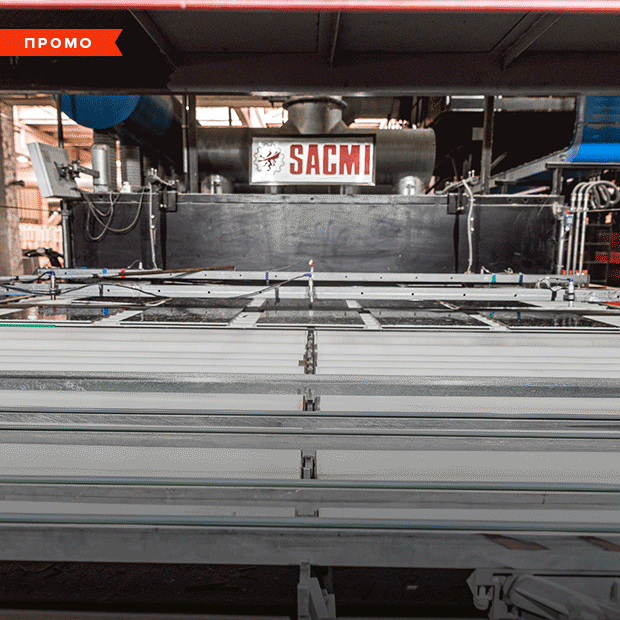
The Village часто рассказывает, как устроены и меняются заслуженные уральские производства. В новом выпуске — Завод керамических изделий, работающий на Вторчермете с 1960 года. К 2019-му производство сменило название на ALMA ceramica, закупило итальянское оборудование и расширило ассортимент до 200 коллекций плитки от классического до лаконичного и урбанистического дизайна. В рамках совместного материала мы побывали на заводе и рассказываем, сколько стадий должна пройти качественная плитка перед тем, как попасть к вам в ванную или на кухню.
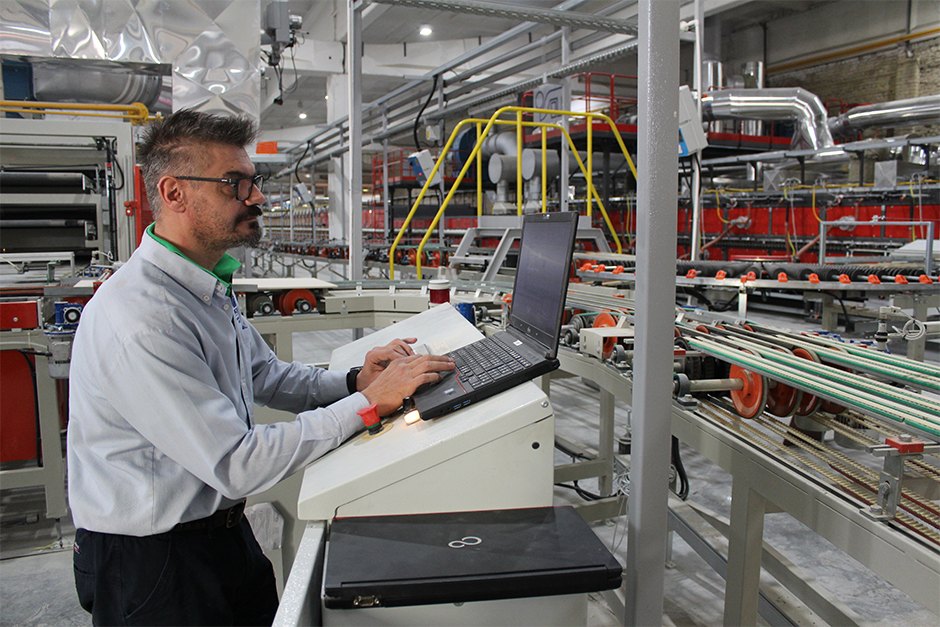
Роботизированные линии
Еще с 1994 года ПАО «ЗКИ» работало по итальянским технологиям, а в 2004-м в цехах запустили три линии с итальянским оборудованием. В 2018-м на заводе наладили уже семь автоматизированных и роботизированных линий полного цикла, в том числе для производства керамогранита (сверхпрочного материала, имитирующего натуральный камень) и декоративных элементов. Новое высокотехнологичное оборудование позволяет производить более восьми миллионов квадратных метров плитки в год. На входе мы видим контейнеры с порошком, а на выходе — ровные ряды коробок ALMA ceramica. Со стороны процесс выглядит, как конвейер, который все делает сам — громко, быстро, чисто и без помощи людей. Их на производстве и правда почти не видно: сотрудники лишь следят за процессами на мониторах и занимаются контролем качества плитки.
1
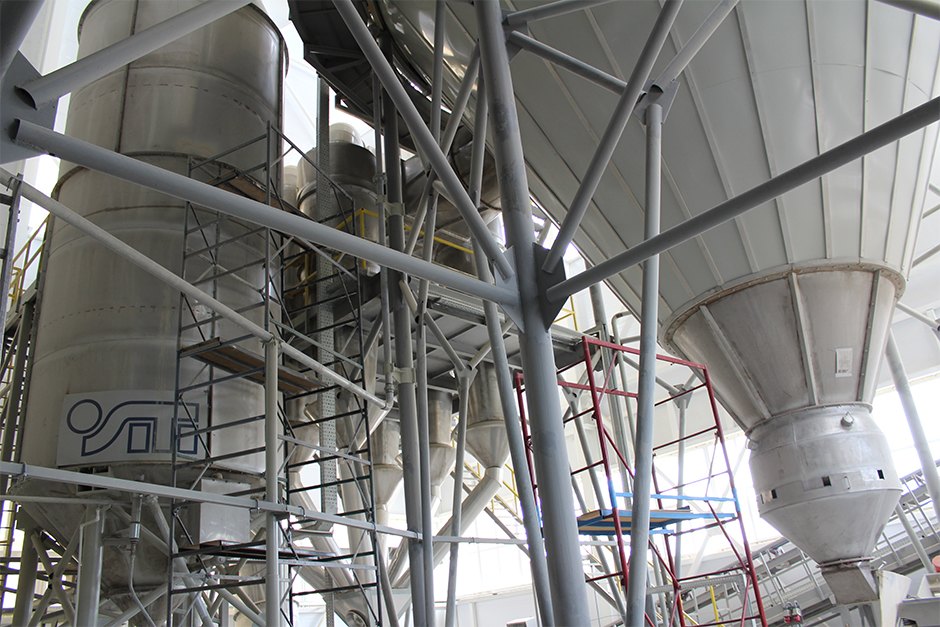
2
Экологичное производство
Свой путь на кухни и в ванные плитка начинает со шликера — смеси из глины и сыпучих материалов. Встреча керамических ингредиентов происходит в гигантской шаровой мельнице. К ним добавляют воду и электролиты, после чего перемешивают и получают этакое глиняное тесто. Суспензию замеряют по определенным параметрам и продолжают непрерывно перемешивать в барабанной мельнице, где каждый барабан весит 40 тонн. На выходе получается шликер. Он отправляется в подземные мешалки, а после на атомизатор, удаляющий из него воду и превращающий в пресс-порошок. Кстати, в состав шликера входит и сломавшаяся плитка. Ее измельчают до состояния порошка и снова пускают в дело, чтобы сократить количество отходов.
3
Хрупкий рельеф
Получившийся порошок попадает в формы и ложится под пресс, где с каждым его ударом получается прототип будущей плитки — появляется необходимый размер и рельеф, — а после отправляется на сушку. Прототип называется сырец и пока очень хрупок, поэтому с ним приходится обращаться максимально осторожно.
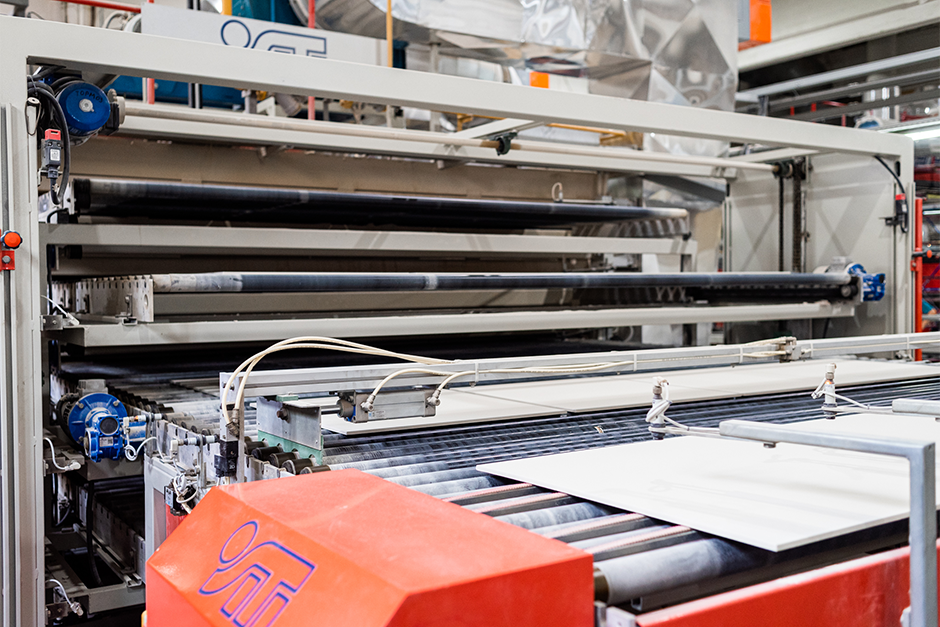
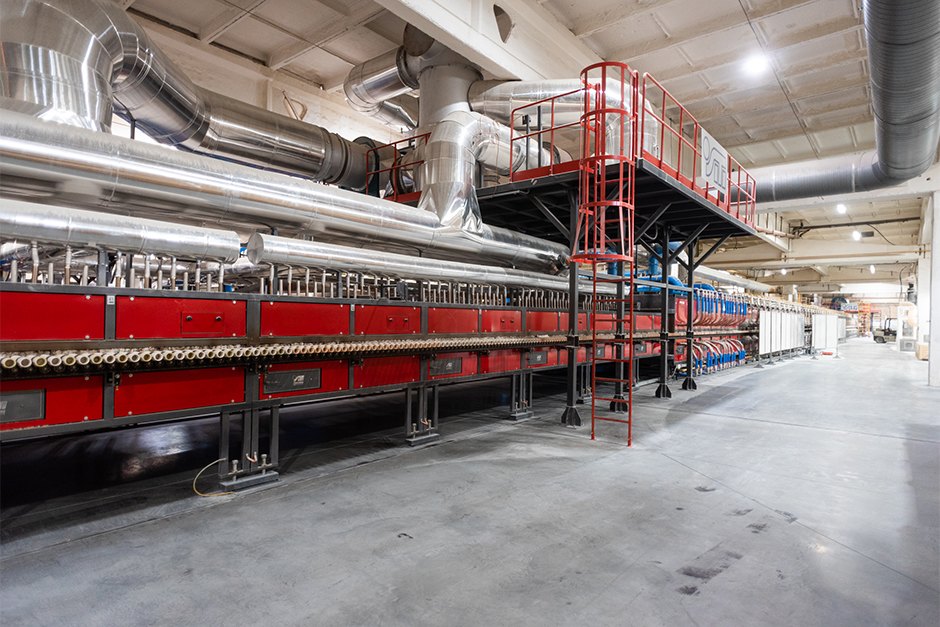
Печь, которую нельзя останавливать
Гигантская печь в несколько десятков метров — сердце цеха. Она дает жар до 1 200 градусов (температура обжига керамогранита) и именно от ее бесперебойной работы зависит беспрерывность производства. Ее остановка грозит остановкой всего — чтобы разжечь печь полностью, понадобится целая неделя. В зависимости от технологии, каждая плитка проходит крещение жаром один (монокоттура) или два раза (бикоттура). Например, тот же керамогранит и напольные покрытия после прессования сушатся и идут в печь один раз. Плитка, созданная по другой технологии, оказывается в печи два раза: до глазурования и после декорирования. Время обжига различается в зависимости от размера плитки. Например, напольная плитка размерами 41 на 41 сантиметр и толщиной в 8 миллиметров томится в печи 35 минут. Крупноформатный керамогранит — почти час.
4
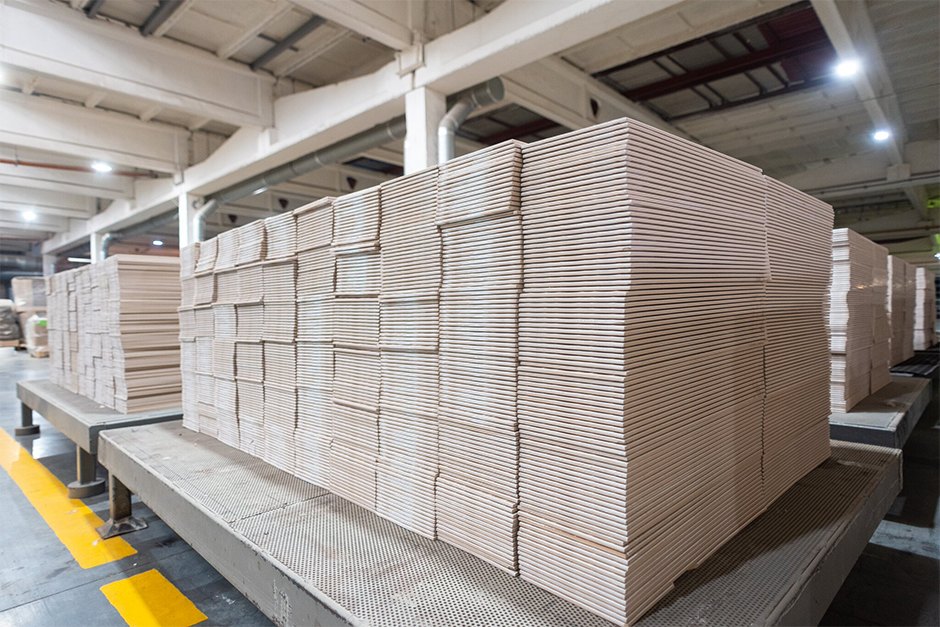
5
Глянцевый щит
Затем на плитку наносят ангоб — керамическое покрытие, придающее плитке белый цвет и выравнивающее ее поверхность. А после — глазурь, которая при обжиге плавится, покрывая плитку глянцевым щитом — водонепроницаемой пленкой.
6
Гигантский принтер и узоры из золота
После глазурования плитка готова обрести «лицо» — получить свой рисунок. Для этого используют четыре масштабные машины цифровой печати, позволяющие наносить на поверхность плитки с рельефом любой сложности изображения высокого разрешения. Дизайнеры ALMA ceramica ориентируются на тренды крупнейших мировых выставок и региональный колорит. Скажем, на Урале покупатели традиционно любят теплые тона, а почти все россияне — декор, поэтому здесь щедро используют глиттер и пасты с эффектами драгметаллов. Кстати, в пастах реально применяют золото (в прошлом году, например, на плитку нанесли 21 килограмм драгоценного металла). Рисунок на продукцию переносится с помощью большого принтера. Если нужна технология двойного обжига, то после этого плитку снова кладут в печь.
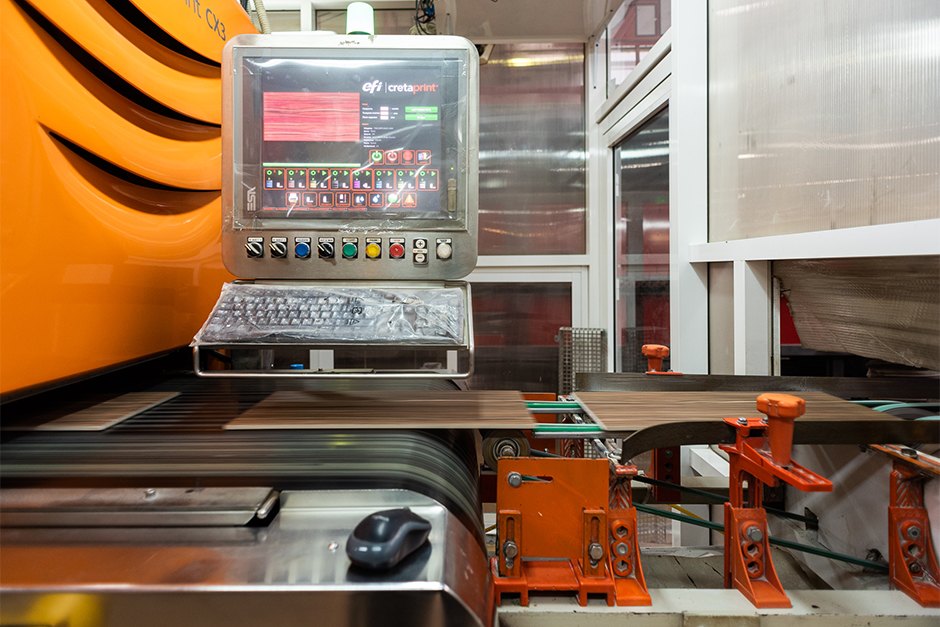

Лед и кипяток
Готовые плитки едут по конвейеру и попадают под небольшое колесо-ролик, с усилием давящее на ее поверхность. Та, что выдерживает, с почетом едет дальше. Изредка слышен хруст и неудачница возвращается на «перевоспитание» в шликер. Следующая проверка — работник с маркером в руках. Специалист помечает плитку неидеального качества, и машина, считывая метку, отправляет ее в начало цикла. В компании гордятся своей плиткой и готовы предоставить все доказательства ее качества. Например, продукцию проверяют на морозо- и влагостойкость. Для первого плитку замораживают, потом опускают в воду для разморозки — проводится много циклов (для гранита не менее 150) и присваивается класс морозоустойчивости в зависимости от того, сколько воды наберет продукция. Для второго плитку кипятят и взвешивают — изменение массы также позволяет присвоить классы для облицовочной, напольной плитки и для керамогранита. Класс помогает покупателям определиться, подходит ли плитка для использования в регионах с капризным климатом.
7
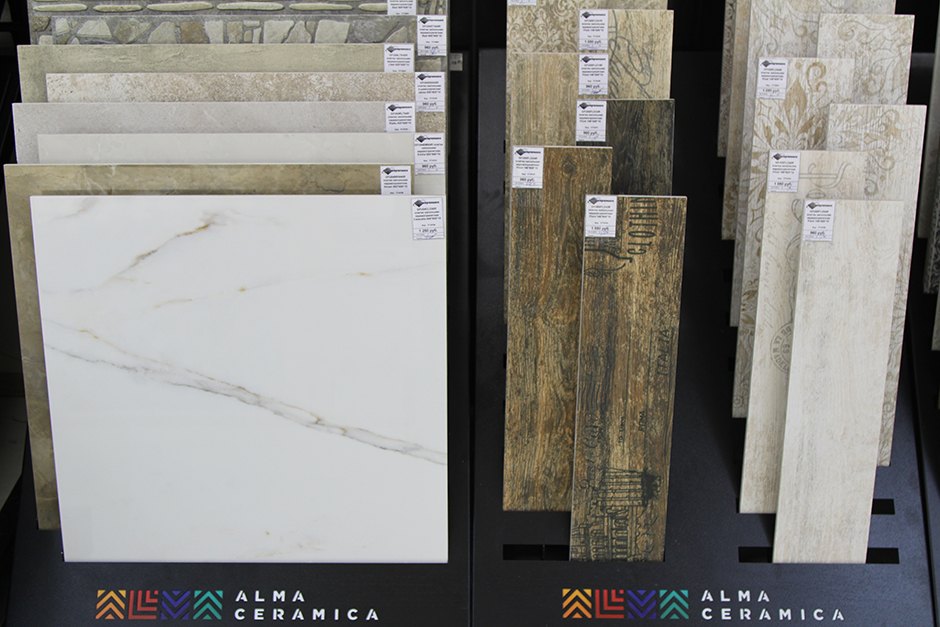
8
Путешествие по России
Готовая плитка на ленте упаковывается в коробки ALMA ceramica с информацией об ее цвете, сорте и калибре, а затем отправляется в магазины. В Екатеринбурге два шоурума марки, также она представлена почти во всех строительных магазинах России и СНГ. Стоимость плитки ALMA ceramica разная в зависимости от коллекции, но в целом они ниже цен конкурентов.