Как делают молочные продукты The Village продолжает узнавать, как производятся разные вещи. На этот раз мы побывали на ферме и молокозаводе братьев Чебурашкиных
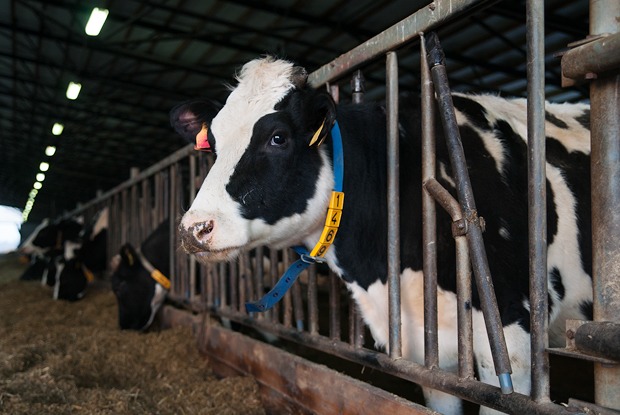
Владислав и Станислав Чебурашкины десять лет назад переехали в Подмосковье из Норильска, где у них был горно-обогатительный бизнес. Здесь они решили вложиться в молочную ферму. Увидев, что продавать молоко переработчикам не слишком рентабельно, они стали устанавливать вендинговые автоматы с ним по городу и области — сейчас работает 35 автоматов «А-Молоко». Кроме того, братья вложились в строительство молокозавода неподалёку от фермы в Дмитровском районе.
Они хотели выпускать молоко под фамильным брендом, но этому мешал Чебурашка: его создатель Эдуард Успенский зарегистрировал товарный знак почти по всем категориям, поэтому с 2011 года Роспатент отклонял заявки на марки «Чебурашкин продукт», «Ферма братьев Чебурашкиных» и другие, ссылаясь на защиту авторских прав. Выиграв суды, в этом году предприниматели запустили производство молочных продуктов «Братья Чебурашкины», которые взяли на полки «Азбука вкуса», «Зелёный перекрёсток» и «Бахетле». Бутылка их молока там стоит дорого — больше 150 рублей за литр. Но на заводе говорят, что оно того стоит: молоко не нормализуют и применяют технологию бережной пастеризации, сохраняющую больше полезных свойств продукта. The Village узнал, как делают такие молочные продукты.
Молокозавод «Братья Чебурашкины»
Расположение: Дмитровский район Подмосковья
Дата открытия: сентябрь 2014 года
Сотрудники: 80 человек
площадь: 2 700 м2
Молоко на завод доставляют с двух ферм: одна находится в Сергиево-Посадском районе, другая — в паре километров от производства, в селе Саввино. На этой ферме сейчас содержатся 1 350 голов скота голштинской молочной породы, из них 610 — дойные коровы.
Круглый год коровы содержатся в стойлах, выходя дважды в день на дойку. В общей сложности она занимает шесть часов. Животные группами по 15 голов заходят в доильное отделение, где доярки протирают им вымя отдельной для каждой коровы салфеткой, сцеживают первые струйки молока и затем надевают доильный аппарат, который начинает отсасывать молоко. По трубам оно поступает в накопитель, коровы уходят в стойло, и их место занимают другие.
В среднем каждая корова даёт по 27 литров молока в сутки. Есть рекордсменки, которые дают больше 40 литров. На ноге каждой дойной коровы есть датчик-респондер, соединённый с базой данных, где хранится информация о её надоях. Кроме того, на ухе коровы есть жёлтая бирка с данными о возрасте и родословной. На шее — порядковый номер, который заменяет корове кличку.
Всего на ферме работают тридцать человек. Здесь есть также отделение для телят: их отлучают от матери почти сразу после рождения и переводят в отдельный бокс. Подросших тёлок оставляют на ферме, бычков отправляют на мясокомбинат.
Полученное от коров молоко проходит через фильтр первичной очистки, а потом поступает в танк-охладитель. Сотрудники фермы определяют массовую долю жира, белка в молоке — оно может быть разным в зависимости от сезона — и отправляют его на молокозавод.
Пока завод перерабатывает по 10−15 тонн молока в сутки, но мощности позволяют перерабатывать до ста тонн. Принимая молоко, сотрудники завода снова его фильтруют и охлаждают, а также проверяют качество. В производственной лаборатории оценивают органолептические, физико-химические и микробиологические свойства продукта на каждом этапе производства.
Вход на предприятие разрешён только в санитарной одежде, необходимо также продезинфицировать руки и вымыть обувь. Здесь есть система цветового кодирования — для каждого цеха свой цвет одежды и инвентаря. Так, красный цвет используется для творожного цеха, где на определённых этапах продукт находится в открытом виде, на фасовке — синий, там сотрудники напрямую не соприкасаются с молоком. Вход в каждый цех — только по специальному электронному пропуску.
Сырьё закачивается в ёмкости вместимостью 30 тонн, где сохраняется постоянная температура от 2 до 4 градусов. Завод работает в две смены: с утра сотрудники разливают заквашенный вечером йогурт, творог и кефир, после полудня — свежее молоко с фермы.
Молоко и кефир здесь цельные, ненормализованные по жиру. Так как каждый день массовая доля жира в молоке разная, на упаковке указывают возможный диапазон, а на крышке, по требованию Техрегламента, — фактическую массовую долю жира именно в этой партии. Для сквашивания кефира используется закваска, приготовленная на живых кефирных грибках. Грибки растут в стерильных боксах на обезжиренном молоке в закрытых ёмкостях.
Для производства других продуктов молоко нормализуют, отделяя сливки с помощью сепаратора: здесь выпускают йогурт с 0,5 % жира, 20-процентную сметану, двух- и девятипроцентный творог. В будущем планируется наладить производство двухслойных йогуртов с вареньем и 40-процентной сметаны.
Из молокохранилища молоко по трубам поступает в приёмный бачок пастеризационно-охладительной установки и после частичного нагрева идёт в сепаратор, который при необходимости отделяет жир, затем — в гомогенизатор. Молочный техрегламент требует обязательной пастеризации продукта. На заводе используют бережную термическую обработку питьевого молока: молоко нагревается до 76−78 градусов, выдерживается при этой температуре 40 секунд, сразу охлаждается до 2−4 градусов и через промежуточную ёмкость идёт на линию розлива. Сотрудники говорят, что это позволяет убить микробы без потери полезных свойств продукта. Правда, такая технология снижает срок хранения молока до семи дней.
Сырьё для кисломолочных продуктов пастеризуют дольше и интенсивнее: в процессе сквашивания в них не должна развиться посторонняя микрофлора. Будущий кефир и йогурт нагревают до 95 градусов, выдерживают при этой температуре пять минут, а потом охлаждают. Для получения йогурта добавляют чистые кисломолочные культуры, для кефира — закваску на кефирных грибках, а потом оставляют сквашиваться на восемь-десять часов. Температура сквашивания у кефира — 18 градусов, у йогурта — 42 градуса.
В оставшиеся от сепарирования сливки добавляют закваску для производства сметаны. Сметану на заводе делают двумя способами. Первый — термостатный, когда заквашенную смесь разливают по стаканчикам, отправляют в термостатную камеру на шесть-восемь часов и потом охлаждают. В такой сметане получается плотный, ненарушенный сгусток — как говорят, «ложка стоит». Второй — резервуарный способ, когда сквашивание происходит в одной ёмкости, а потом идёт охлаждение, перемешивание и фасовка уже готовой сквашенной сметаны.
Творог тоже сквашивается кисломолочными бактериями. Чтобы произвести килограмм продукта, нужно шесть килограммов молока. В производстве не используется сычужный фермент, поэтому творог подходит вегетарианцам. После сквашивания и частичного охлаждения творожный сгусток по трубам подаётся в барабан-отделитель. Через его отверстия выходит сыворотка, а творог поступает в туннель с холодным озонированным воздухом, где охлаждается до 10−12 градусов. Благодаря этому кислотность творога не увеличивается в процессе хранения.
Молоко и молочные продукты на заводе разливают в пластиковые ПЭТ-бутылки. Их производят на соседнем с цехом розлива участке: выдувают из преформ, затем подают на конвейер, промывают и заполняют продуктом. Автомат закручивает крышку и наклеивает этикетку. Уже на выходе рабочие надевают бирку с информацией о компании. Бренд «Братья Чебурашкины» пока не очень известен на рынке, многие думают, что семейная ферма — это просто маркетинговый ход и таких предпринимателей на самом деле нет, так что владельцам приходится прикладывать к каждой бутылке молока и кефира своё фото.
После розлива бутылки молока упаковывают по шесть штук и увозят на склад, откуда они и другие продукты компании поставляются на прилавки магазинов.
Фотографии: Глеб Леонов
Чтобы прочитать целиком, купите подписку. Она открывает сразу три издания
месяц
год
Подписка предоставлена Redefine.media. Её можно оплатить российской или иностранной картой. Продлевается автоматически. Вы сможете отписаться в любой момент.
На связи The Village, это платный журнал. Чтобы читать нас, нужна подписка. Купите её, чтобы мы продолжали рассказывать вам эксклюзивные истории. Это не дороже, чем сходить в барбершоп.
The Village — это журнал о городах и жизни вопреки: про искусство, уличную политику, преодоление, травмы, протесты, панк и смелость оставаться собой. Получайте регулярные дайджесты The Village по событиям в Москве, Петербурге, Тбилиси, Ереване, Белграде, Стамбуле и других городах. Читайте наши репортажи, расследования и эксклюзивные свидетельства. Мир — есть все, что имеет место. Мы остаемся в нем с вами.